Production Process
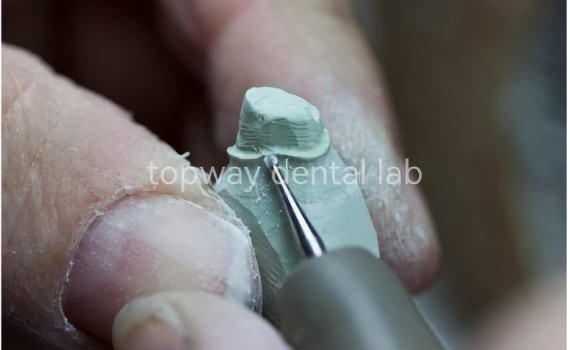
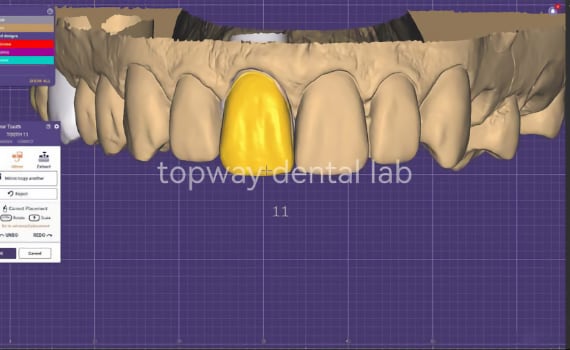
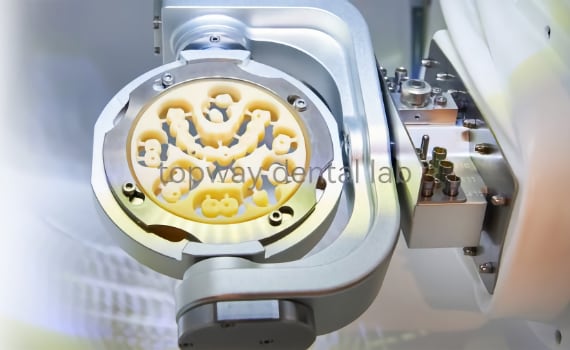
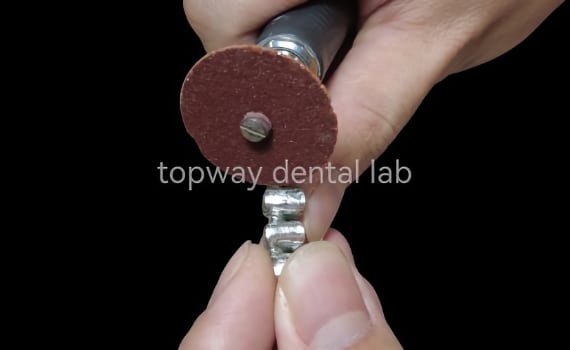
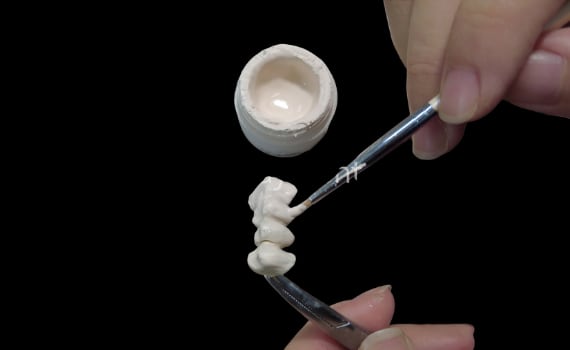
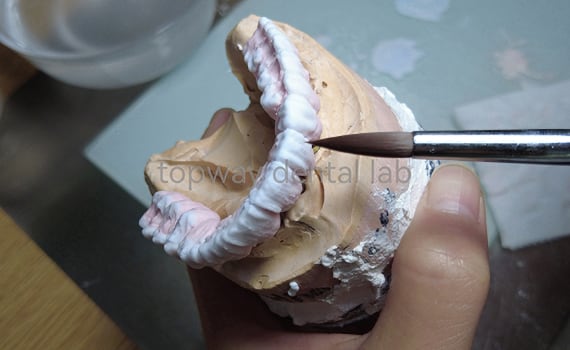
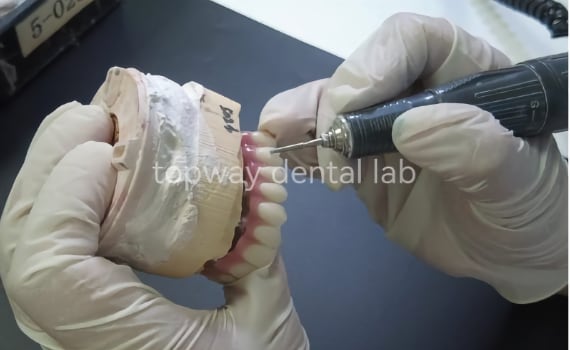
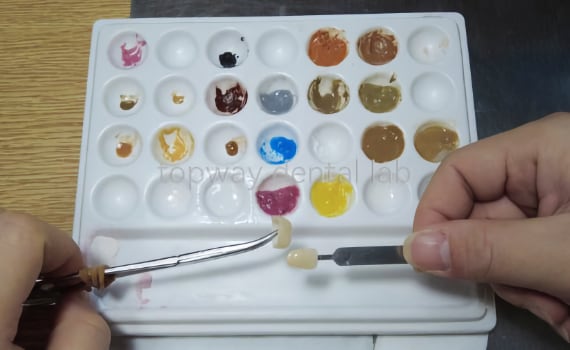
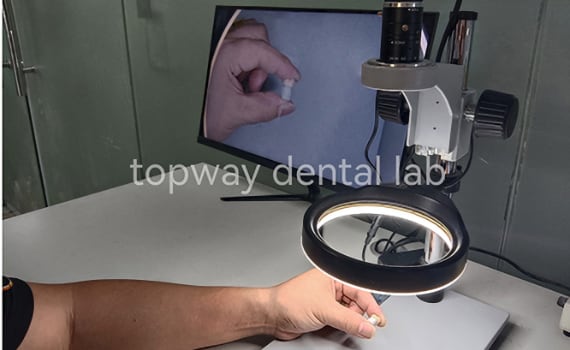
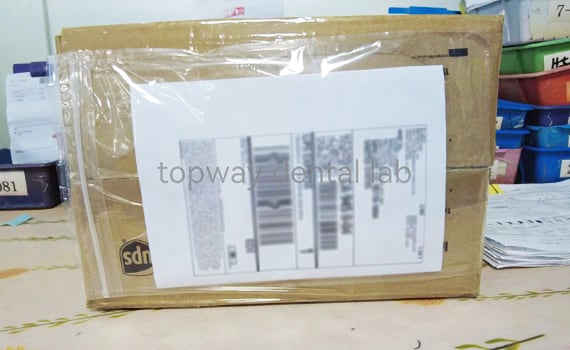
Dental Service Turnaround Time
Fixed Crown & Bridges | In Lab Days |
---|---|
PFM Crown & Bridge <4 units | 3-4 days |
PFM Crown & Bridge >4 units | 4-5 days |
Metal Try-in / Full Cast Crown | 2 days |
Porcelain Finish | 2-3 days |
Post & Core+PFM | 3-4 days |
Temporary Crown & Bridge | 2 days |
E-max Crown & Veneer | 3 days |
Zirconia Crown & bridge <4 units | 3-4 days |
Zirconia Crown & Bridge >4 units | 4-5 days |
Full Contour Zirconia Crown & Bridge<5 units | 2-3 days |
Full Contour Zirconia Crown & Bridge>5 units | 3-4 days |
Implant Crown & Bridge<4 units | 4 days |
Implant Crown & Bridge>6 units | 5-6 days |
Implant Crown & Bridge>6 units | 5-6 days |
Removables | In Lab Days |
---|---|
Cast framework | 2-3 days |
Cast framework with Wax Rim | 2-3 days |
Cast framework with set up | 3-4 days |
Cast framework with denture finish | 4-5 days |
Set up only | 2-3 days |
Finish denture | 2-3 days |
Set up and finish | 3 days |
Fixed Combo with Removable | In Lab Days |
---|---|
Fixed & Cast only | 2-3 days |
Fixed & Cast and denture | 3-4 days |
Tooth Box Classification

The order tracking group places the dental lab cases in the corresponding boxes according to the shipping time.
Production is carried out in sequence according to the color of the boxes.
Shipping Management
The Group will record customers and their respective delivery times for the next day on the shipping whiteboard.
The Group will communicate the shipping schedule to the Production Department for alignment.
The Production Department will organize the production sequence for each customer according to the scheduled shipping times.
Quality control will inspect the products to ensure they meet required standards.
Products will be packaged and labeled correctly for each customer based on the shipping schedule.
Finally, products will be moved to the shipping area or loaded onto delivery vehicles as per the scheduled times.
Shelf Management
3 types of cases: question cases, remake cases, urgent cases are placed on the top shelf for technicians to allocate and produce them as quickly as possible.
Unfinished dental cases are placed on the shelf in order of their shipping dates, from top to bottom.
The team leader starts allocating dental cases from the topmost layer.
Order Tracking - System Management
- The corresponding process in which it is located.
- Corresponding production order number
Each item can be traced to its corresponding production process, producer, and completion time.
The tracking clerk will monitor the progress of each item in the customer's package.
The customer provides an urgent list, and the document clerk tracks the progress of urgent dental cases until they are shipped on time.
Quality & Progress Assurance
Our process starts with the Tracking Department issuing a production plan. Dental cases are sorted into specific shipping boxes based on customer deadlines. Distinct colors indicate different shipping times, ensuring orders are prioritized correctly from the outset for timely completion.
Teams process cases in the specified sequence from designated shelves. Team leaders handle urgent items and manage smooth handovers to the next stage. The entire workflow is monitored by video surveillance, ensuring every production step is controllable and fully traceable for quality assurance.
Tracking clerks calculate the on-time shipping rate by comparing planned versus actual shipment times. They compile lists of any delays. Production assistants then investigate the root causes for these delays, analyzing performance and pinpointing responsibility down to the team level.
Production clerks summarize daily delays and track the progress of each team's output. This data directly informs the assessment of team leaders' management performance. This evaluation impacts their reviews, fostering accountability and driving continuous improvement efforts.
Production Quality Management
Arrival Inspection
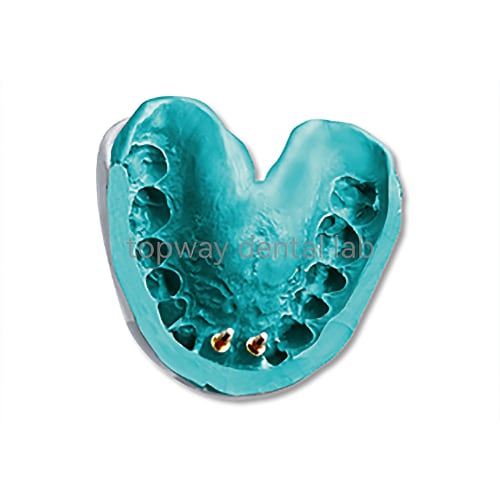
Inspection of implant components
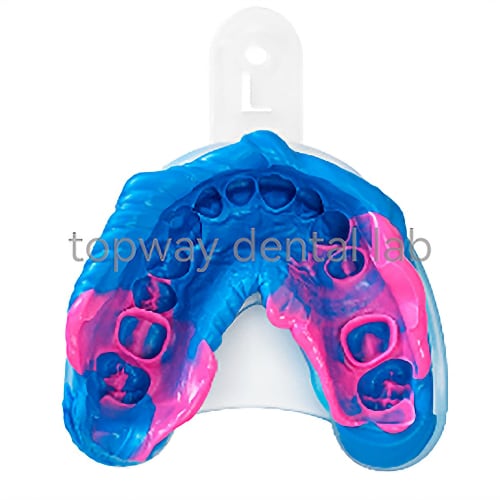
Inspection of the Prep teeth and margin
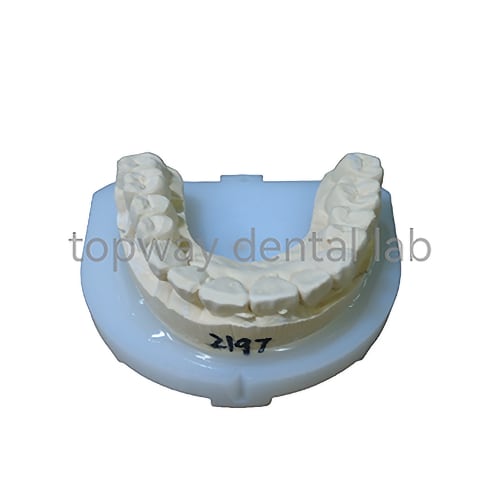
Inspection of the model
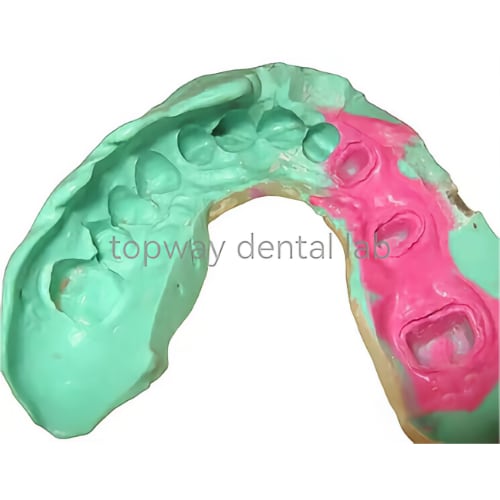
Inspection of the wax bite
Process Inspection
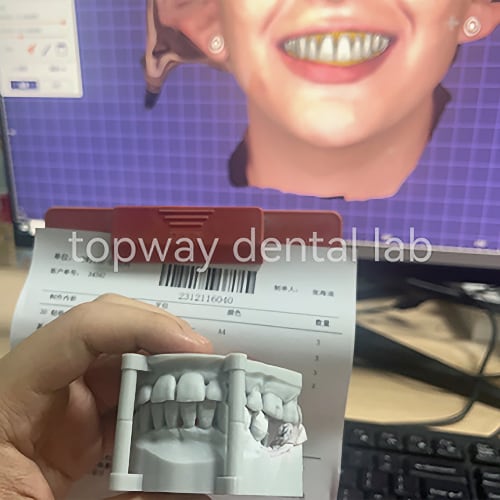
Pre-design bite check
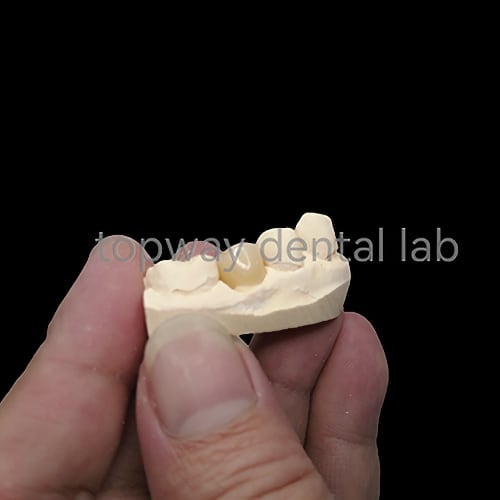
Check the fit
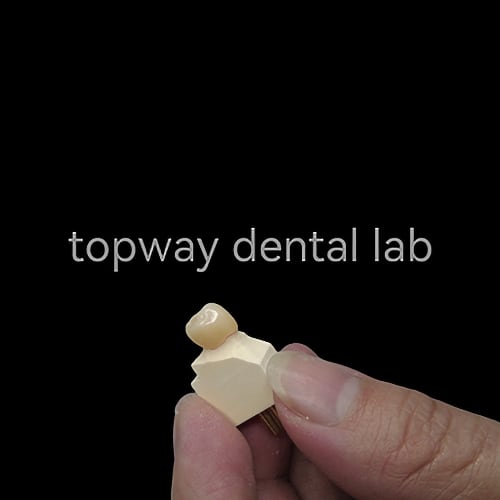
Check the margin
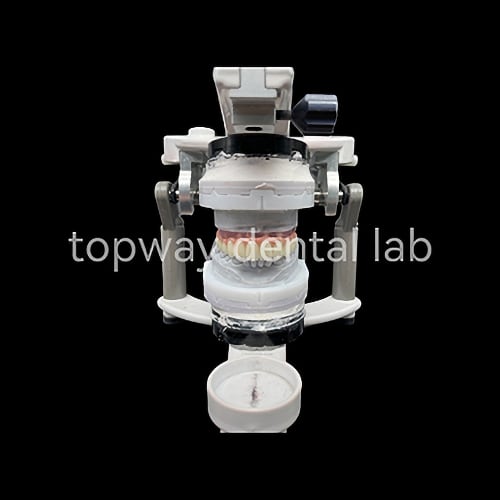
Bite check when mill porcelain
Final Quality Inspection
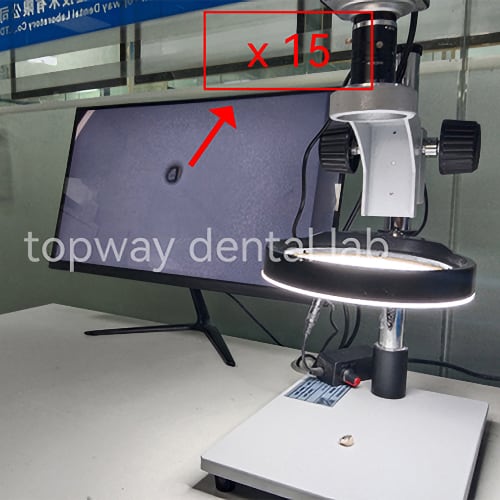
Check fit
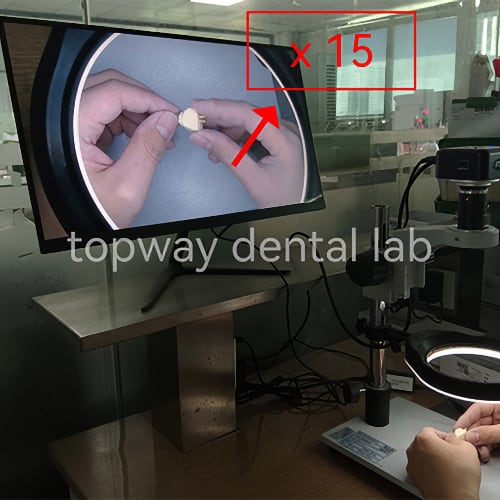
Check margin
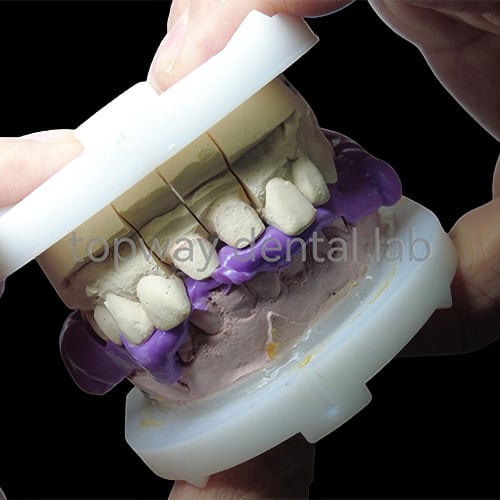
Check the occlusion
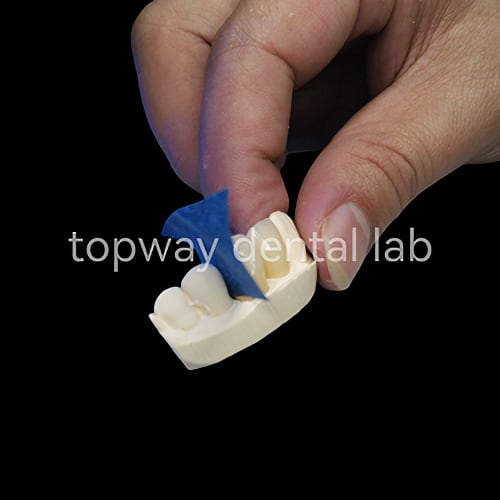
Check contact
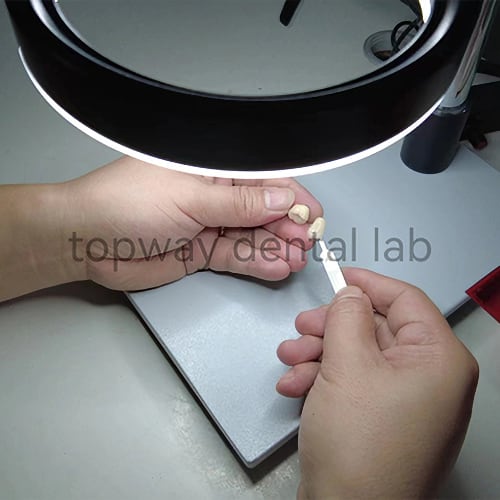
Check the shade
Quality Inspection Standard Grades
- Perfect edge fit, no overhang, no underlying color
- Perfect positioning
- Vivid form
- Good color layering
- Surface without defects
- Bite contact meets customer requirements
- No functional defects, perfect arrangement
- Rough
- Bubbles, small holes, black spots
- Slightly misaligned
- Missing porcelain in long bridge tooth gaps, minor edge chipping
- Not made according to design requirements
- Unable to be positioned
- Incorrect edges
- Incorrect color
- Deformed